Leuven, 15 december 2021. Toen de Vlaamse Landmaatschappij (VLM) de aandacht van bezoekers wilde vestigen op een oude dispersal of militaire open bunker voor stalling van vliegtuigen in Honsem (Boutersem), zochten ze een ankerpunt voor de geplande ontwikkeling van het landelijke landschap. Iets dat het historische belang zou tonen dat het gebied tijdens de Tweede Wereldoorlog had.
Een levensgroot model van een Belgisch verkenningsvliegtuig uit de jaren dertig, de Renard R31, was een goede keuze. Om hun visie werkelijkheid te laten worden, ging VLM in zee met Materialise Manufacturing om het model uit te voeren met behulp van 3D-printen (zie databank https://www.hangarflying.eu/erfgoedsites/artistieke-replica-van-de-renard-r31/).
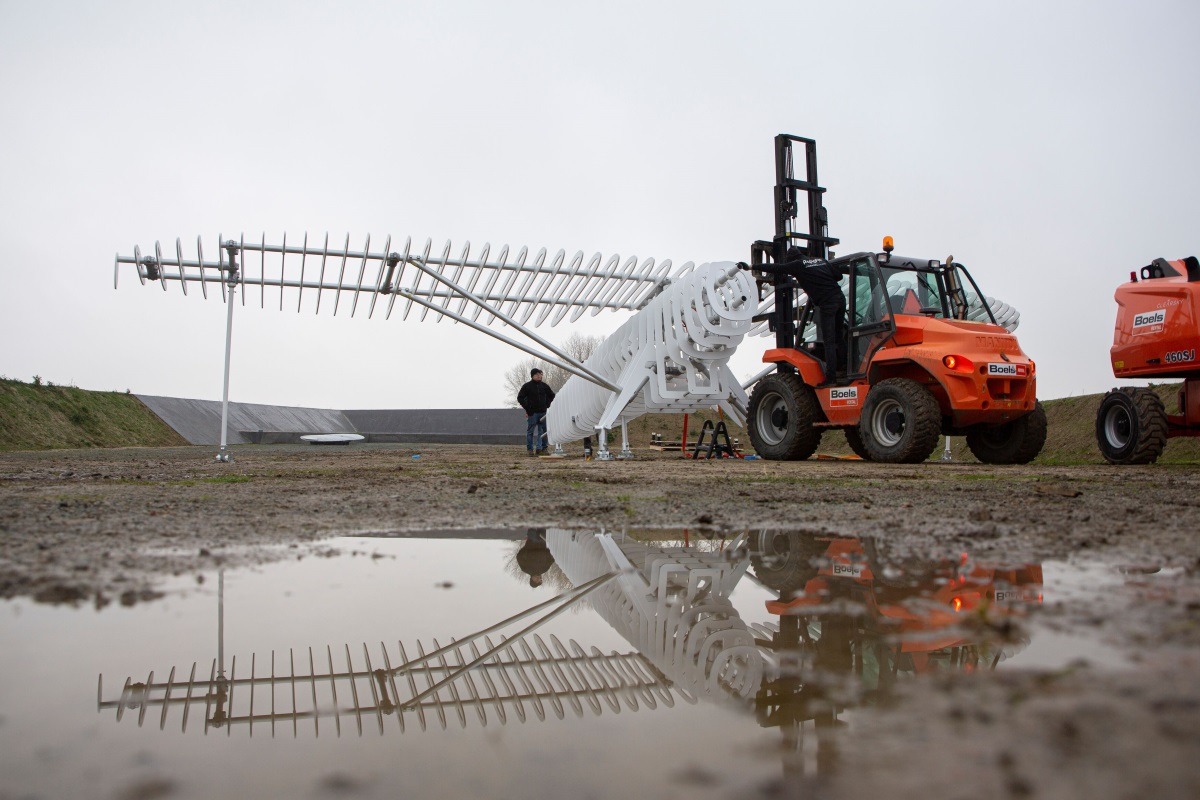
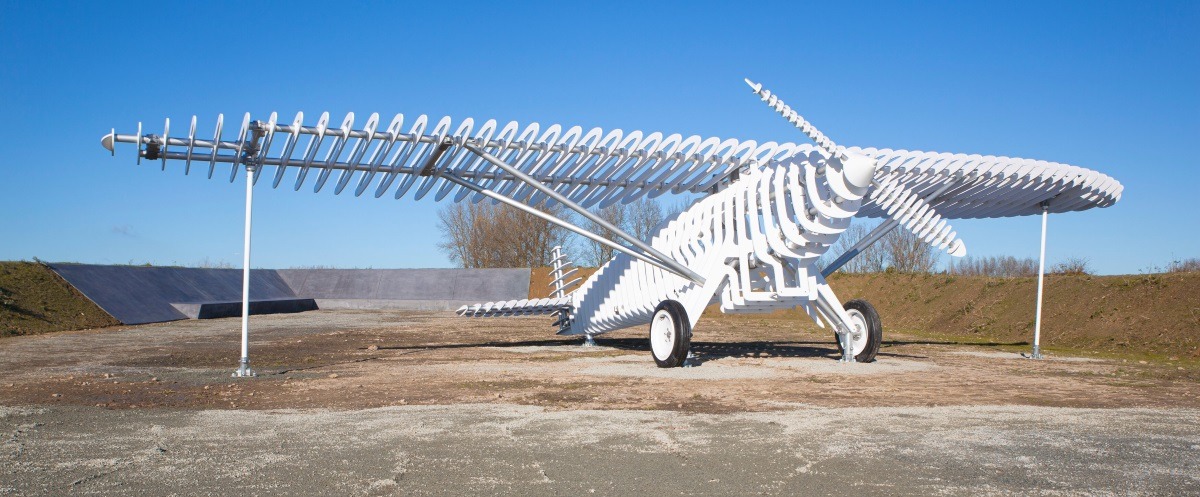
Leuk en met de tijd mee, nietwaar? Materialise is echter veel meer. Gelegen aan de rand van Leuven, is Materialise al meer dan 30 jaar een naam als een klok in industrietakken als automotive, gezondheidszorg, consumptiegoederen, kunst en design, en luchtvaart.
Materialise heeft vestigingen over de hele wereld, de grootste groep softwareontwikkelaars in de branche en een van de grootste 3D-printfaciliteiten ter wereld. Het produceert 700 onderdelenseries per jaar voor lucht- en ruimtevaartklanten, van Original Equipment Manufacturer (OEM) tot Maintenance, Repair and Overhaul (MRO) en leveranciersniveaus, waaronder naar schatting 26.000 onderdelen per jaar alleen al voor het de Airbus A350.
R&D en MRO in de 21e Eeuw
De belangstelling voor de on-site en on-demand mogelijkheden voor het maken van onderdelen en componenten met Additive Manufacturing (AM) en 3D-printen is wijdverbreid in de lucht- en ruimtevaartsector – van OEM’s tot MRO’s en de opkomende sector voor stedelijke luchtmobiliteit (Urban Air Mobility, UAM).
Het bedrijf is momenteel de enige leverancier die productiediensten aanbiedt in twee 3D-printtechnologieën die door Airbus zijn goedgekeurd voor vluchtklare onderdelen, en werd in mei 2021 de eerste fabrikant van Airbus voor de Selective Laser Sintering (SLS)-technologie.
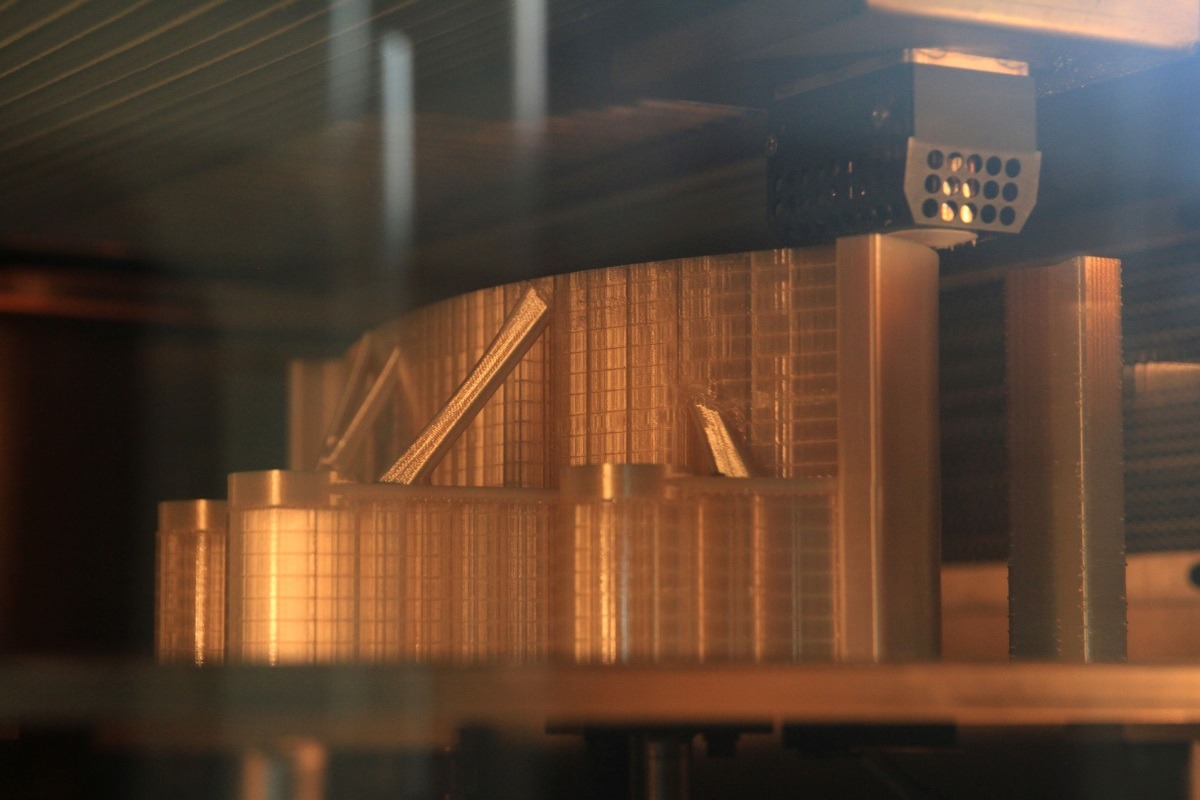
Materialise kondigde vorig jaar op MRO Europe 2021 in Amsterdam een samenwerking aan met Proponent om de toeleveringsketens voor de lucht- en ruimtevaart-aftermarket te transformeren met 3D-printen. Proponent, met hoofdkantoor in Californië, is de go-to distributeur van vliegtuigonderdelen en levert traditionele distributiediensten aan luchtvaartmaatschappijen, MRO’s en OEM’s, evenals oplossingen voor voorraadbeheer. Het bedrijf levert 54 miljoen onderdelen per jaar aan meer dan 6.000 luchtvaartklanten in meer dan 100 landen.
Erik de Zeeuw, Aerospace Market Manager van Materialise sprak recent met Farnborough International over hoe luchtvaartbedrijven momenteel 3D-printen en Additive Manufacturing (AM) gebruiken en het grotere potentieel dat deze technologieën kunnen bieden. Een beknopte weergave van het gesprek:
Uw bedrijf is al sinds de begindagen van de technologie bezig met additieve productie. Kunt u een overzicht geven van de ontwikkelingen op het gebied van vluchtklare 3D-geprinte onderdelen sinds de oprichting van Materialise in 1990?
Erik de Zeeuw: “Vroeger begon een project met rapid prototyping, dus we printten prototypes voor nieuwe ontwikkelingen die conventioneel zouden worden vervaardigd. Prototyping was een eerste killer-applicatie van 3D-printtechnologie omdat het een snelle manier is om ontwerpen te valideren. Het is nog steeds een groot deel van onze activiteit, maar in de loop der jaren is de technologie volwassen geworden en heeft vandaag de dag erkende voordelen als fabricagetechniek voor eindgebruiksonderdelen.
Rond 2014/15 bereikten we een keerpunt: we werden door Airbus benaderd om een gekwalificeerde leverancier voor hen te worden. We leverden ook onze eerste onderdelen aan andere OEM’s en MRO-bedrijven en ontvingen twee kwalificaties – EN9100 en EASA 21.G – waarmee we gecertificeerde vliegende onderdelen konden produceren. Binnen de lucht- en ruimtevaart zijn de series kleiner en zijn de voordelen van lichtgewicht AM veelbelovend, dus dit is een industrie met groeiende belangstelling binnen dit vakgebied.”
Problemen met de toeleveringsketen zijn momenteel een hot topic. Welke rol speelt additieve fabricage bij het verlichten van deze problemen?
Erik de Zeeuw: “AM zelf heeft tijdens de pandemie niet noemenswaardig geleden onder de algemene tekorten in de toeleveringsketen; op dit moment vertegenwoordigt additief slechts een klein deel van de productiemarkt en wordt het gebruikt met specifieke materiaalkwaliteiten. Aan de andere kant werd AM wel een oplossing voor andere industrieën om tekorten op te lossen; het is een alternatieve manier om specifieke onderdelen on demand en lokaal te produceren, waar traditionele productie en buitenlandse leveranciers niet konden leveren vanwege de covidcrisis.”
Kunt u enkele voorbeelden geven van de meest populaire lucht- en ruimtevaartonderdelen die worden vervaardigd?
Erik de Zeeuw: “Er zijn ruwweg twee categorieën: aan de ene kant heb je ‘superhelden’-applicaties, heel moeilijk te realiseren en gecertificeerd te krijgen, maar dit zijn degenen die alle media-aandacht krijgen. Een populair voorbeeld hiervan werd gemaakt door General Electric. Ze zagen het potentieel om AM te gebruiken om complexe metalen onderdelen in de motor te vervaardigen om het gewicht te verminderen en om onderdelen te combineren. Ze hebben enorm veel middelen in dit product gestoken, maar het is zeer succesvol geweest in die zin dat het de voordelen van AM heeft laten zien bij het verminderen van het gewicht, het verminderen van componenten en het toevoegen van functionaliteit, alles in een applicatie die veilig kan vliegen.
De andere categorie zijn de ‘onbezongen’ helden. Het is nu mogelijk om onderdelen met een lage of niet-kritische waarde te maken met behulp van Additive Manufacturing . En dit zie je bijna overal in het vliegtuig, vooral in het interieur van de cabine, bijvoorbeeld uitstapborden of pennenhouders. Het merendeel van de onderdelen die wij produceren, bevinden zich op dit gebied. Hier worden de ontwerpvoordelen AM nog niet volledig benut- de ontwerpen zijn in wezen hetzelfde als bij traditionele productie – maar het biedt wel supply chain-voordelen. Op de aftermarket hebben luchtvaartmaatschappijen bijvoorbeeld doorgaans maar een paar van elk onderdeel nodig, maar conventionele fabricage zou hen dwingen tot grote minimale bestelhoeveelheden die ze vervolgens in voorraad moeten hebben. AM maakt seriegroottes mogelijk vanaf één exemplaar. Dit soort laag kritische applicaties zijn ook een goede manier voor lucht- en ruimtevaartbedrijven om aan de technologie te wennen en vervolgens stap voor stap op te schalen naar producten met een hogere kritische factor.”
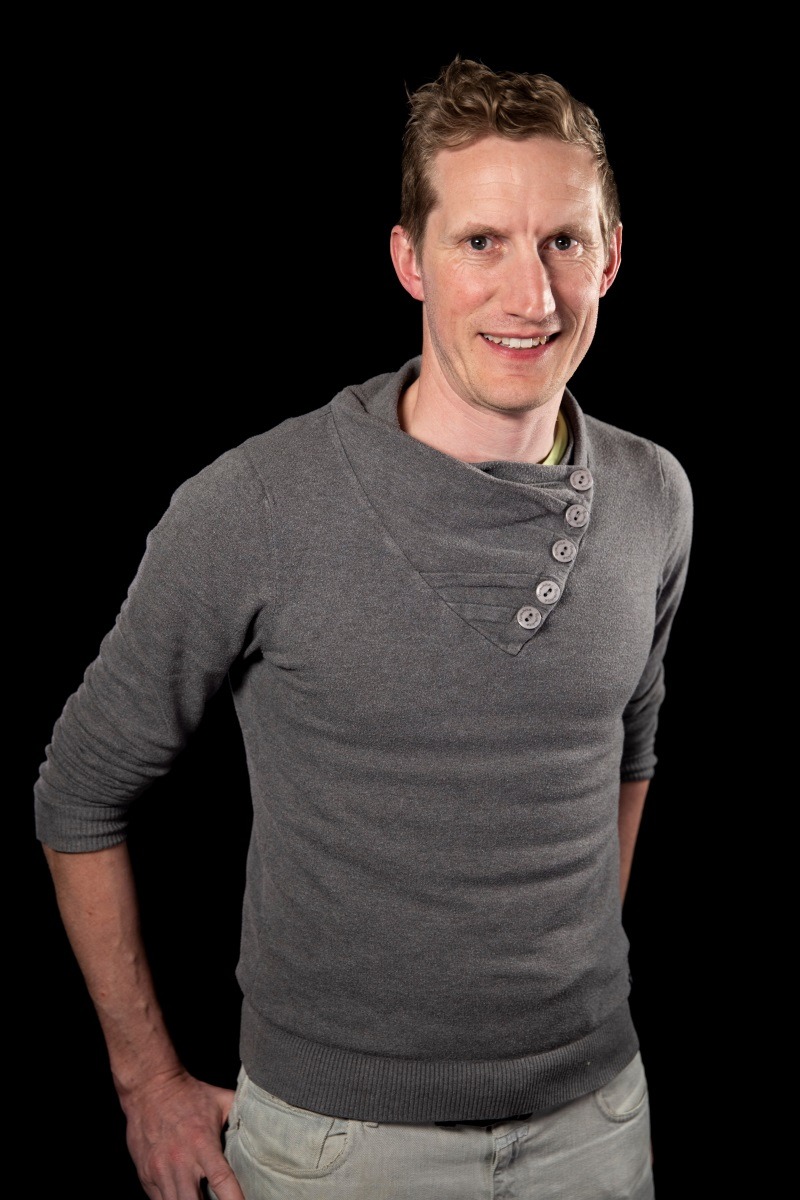
Kunt u uitleggen hoe de technologie de ontwikkeling van de stedelijke luchtmobiliteit/UAV-sectoren kan ondersteunen?
Erik de Zeeuw: “Er is een race to the sky met een enorm aantal projecten in dit segment, die allemaal in de komende twee tot vijf jaar de vliegtuigproductie willen starten of certificering willen behalen. Er is een voortdurende productontwikkeling met een behoefte aan iteraties, prototypes, brugfabricage, alle dingen die AM zou kunnen leveren. Dat is het geval met het Lift-vliegtuig, waar we 3D-printen gebruikten om een eVTOL-vliegtuig in iets meer dan een jaar van een vel papier tot een bemande vlucht voor onze klant te itereren.” Lees hieronder meer over het project, ‘eVTOL startup LIFT Aircraft en haar radicale missie: vliegen democratiseren.’
Erik de Zeeuw: “Urban air mobility-vliegtuigen gebruiken doorgaans elektrische voortstuwing, wat betekent dat ze zo licht mogelijk moeten zijn om het maximale uit de batterijen te halen. Lichtgewicht betekent bijna standaard complex: denk aan traliewerkinterieurs en topologisch geoptimaliseerde onderdelen, in tegenstelling tot een massief blok. Het verzekeren van de eigenschappen van onderdelen, testen en inspecties in deze omgeving is ook navenant complex. Het is dus begrijpelijk waarom regelgevers terecht voorzichtig zijn. Tegelijkertijd zijn de voordelen van AM in deze toepassing duidelijk. Je ziet het potentieel van AM in die markt worden toegepast, het komt zeker in de toekomst.”
Vooruitkijkend naar de rest van het decennium, welke veranderingen of problemen verwacht u te zien binnen additive manufacturing?
Erik de Zeeuw: “Binnen de lucht- en ruimtevaart is het niet eenvoudig om een ontwerp te maken en te certificeren. Additive manufacturing is een zeer gevoelig proces – er zijn veel factoren die de kwaliteit van een product beïnvloeden en al deze factoren moeten worden gecontroleerd. De kennis staat nog in de kinderschoenen. We weten wat we moeten doen, maar het is erg intensief en je moet heel streng zijn om het goed te doen.
Waar bedrijven en regelgevende instanties naar op zoek zijn, is verbeterde procesbeheersing. Om een output te hebben die zeer stabiel en voorspelbaar is, is nog veel ontwikkeling nodig. Dit is een probleem voor bedrijven die 3D-printen willen toepassen, maar de hele industrie is gefocust en werkt hieraan specifiek voor de lucht- en ruimtevaart. Dit is iets in het komende decennium dat zal evolueren en, stap voor stap, zal rijpen. Bij Materialise hebben we al stappen ondernomen om het genereren van gegevens te standaardiseren en ons datameer open te stellen voor onze luchtvaartpartners om te helpen bij hun kwalificatie-inspanningen.
Wat de materialen betreft, heeft de industrie tot nu toe gebruik gemaakt van materialen die vliegwaardig zijn, maar die voornamelijk zijn ontworpen door de AM-industrie. Materiaalontwikkeling voor 3D-printen is nogal complex, maar er zijn meer materialen die passen bij specifieke ruimtevaartbehoeften: hoogwaardige polymeren, meer specifieke metaallegeringen, zijn zaken die in ontwikkeling zijn.
Het zou best intensief zijn om bestaande onderdelen te vervangen door 3D-printen, maar ik verwacht dat als je bij clean sheet vliegtuigontwikkeling komt, daar steeds meer over nagedacht zal worden. Onze ultieme hoop is dat AM zal worden beschouwd als een technologie die zal worden gebruikt wanneer je een complex onderdeel of onderdeel in een kleine serie nodig hebt, zodat het niet meer iets speciaals is. Het personeel zal echter moeten worden opgeleid. Ontwerpingenieurs enzovoort, zullen moeten begrijpen hoe het werkt en wat het kan doen.”
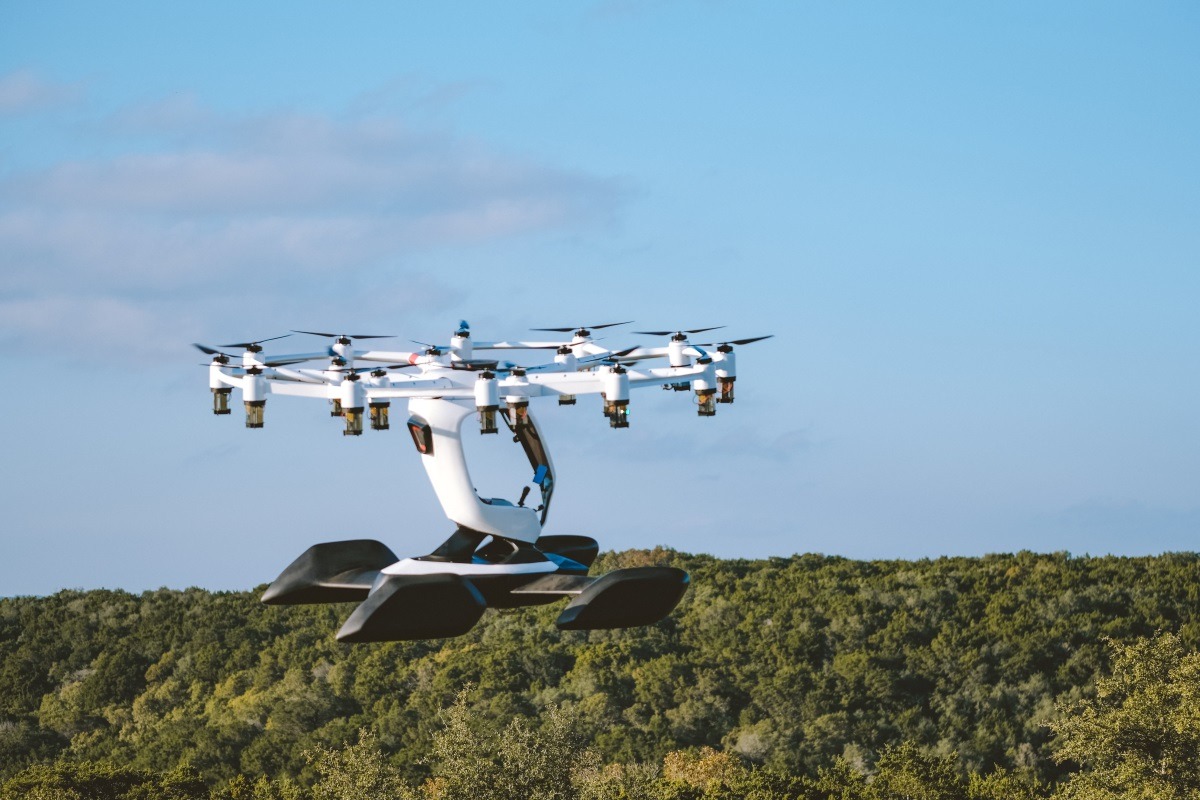
Hoe wordt de factor duurzaamheid van additive manufacturing bij Materialise vergroot?
“De gekende boodschap rond AM is dat je gewoon print wat je nodig hebt en in die zin is AM een duurzame technologie. Maar de echte boodschap is ‘hoe kunnen we AM duurzamer maken?’ Samen met andere 3D-printbedrijven zijn we zeer arbeidsintensief met speciale materialen die niet vrij zijn van impact.
We hebben duurzaamheid gedefinieerd als een belangrijke strategische component en hebben verschillende methodieken toegepast om dat aan te pakken. We hebben onze jaarlijkse rapportage over duurzaamheid verhoogd, volgens het UN Global Compact, verschillende milieubeheermethodologieën aangenomen, zoals ISO 14000, en van die reactieve benadering zijn we geëvolueerd naar een proactieve aanpak.
We hebben ons ertoe verplicht om op wetenschappelijke gebaseerde basis (https://sciencebasedtargets.org/) onze uitstoot tegen 2025 te halveren. Dit zijn acties die we op verschillende niveaus ondernemen, dus het is ingebed in onze managementsystemen, gestructureerd en is behoorlijk ambitieus. Recente verwezenlijkingen waren een circulaire verbetering van ons meest gebruikte polymeermateriaal, een nieuw vliegreisbeleid dat vluchten verbiedt voor afstanden korter dan 400 kilometer. We zijn ook bezig om al onze kantoren wereldwijd tegen eind 2022 van groene energie te voorzien. Er zijn verschillende acties gericht op een groot globaal plan.
De milieurapportage is niet iets dat we op dit moment ervaren als een druk van onze luchtvaartklanten, maar het komt meer van onze investeerders, binnen bepaalde verticale markten, van onze consumenten en niet in het minst van ons eigen personeelsbestand. »
eVTOL start-up LIFT Aircraft en haar radicale missie: vliegen democratiseren
LIFT Aircraft Inc. is een in de VS gevestigd eVTOL-bedrijf (electric Vertical Take-Off and Landing) met een wereldwijd team en een eenvoudige missie: de ervaring van het besturen van een piloot voor iedereen toegankelijk maken. Het team rond CEO Matt Chasen heeft geavanceerde technologie gebruikt, van batterijen tot materialen, van generatief ontwerp tot additieve productie, om in minder dan dertien maanden van een blanco vel papier naar een bemande vlucht te gaan. We praten met CEO Matt Chasen, hoofdingenieur Balazs Kerulo, en Charles Justiz, een voormalig NASA-testpiloot, over de rol die 3D-printen tot nu toe heeft gespeeld in hun reis en hoe ze steeds de juiste balans vinden tussen snel en veilig.
Je begon meteen met een duidelijk businessmodel. Dit was geen gekke uitvinder aan het werk – jullie hadden van de start een duidelijke strategie om dit in serieproductie te nemen.
Matt Chasen: “Dat klopt. We begonnen niet zomaar aan een tienjarig R&D-project. We gingen eerst op zoek naar een echte zakelijke kans. Wat we vonden was deze regelgevende klasse in de VS genaamd ‘ultralichte vliegtuigen’. De uitdaging is om te voldoen aan de gewichtsbeperkingen van die klasse. We zijn hierin geslaagd door gewichtsoptimalisatie van 3D-printen en andere technologieën. Het stelde ons in staat om naar de markt te gaan zonder certificering van EASA – en er is niet eens een vliegbrevet vereist! In termen van onze missie om de vlucht te democratiseren, is het gewoon perfect.”
Je kwam ongelooflijk snel bij je eerste prototype. Ben je van plan dat vol te houden?
Matt Chasen: “Ja! We gebruikten 3D-printen om een vliegtuig in iets meer dan een jaar van een blanco vel papier naar een bemande vlucht te itereren. We hebben dat gedaan door veel van de onderdelen die nodig zijn voor onze verschillende prototypes in 3D te printen, die vervolgens zeer snel evolueerden tot een van de allereerste productie-eVTOL-vliegtuigen ter wereld.
En dat tempo willen we vasthouden. In de luchtvaart heb je met gecertificeerde vliegtuigen doorgaans extreem lange productcycli. Want als je eenmaal iets hebt ontwikkeld en gecertificeerd, is het zo ontzettend moeilijk en duur om dat te veranderen of iets nieuws te doen. Dus je blijft maar hetzelfde doen. De luchtvaart wordt hierdoor echt tegengehouden om vooruit te komen.
Andere industrieën vinden opnieuw uit en herhalen, en je ziet productcycli in technologie die veel sneller zijn! Omdat certificering niet vereist is, kunnen we streven naar productcycli die veel dichter liggen bij wat we in de techsector zien. We streven naar een cyclus van twee à drie jaar, in plaats van twintig tot dertig jaar, wat nu typisch is in de luchtvaartindustrie. En een deel van wat dat mogelijk maakt, is 3D-printen.
Met additieve productie hoef je niet te investeren in grote hoeveelheden bestellingen waarvoor mallen en al die dure dingen nodig zijn die alleen zinvol zijn als u tienduizenden van iets nodig heeft. Als we maar duizend van iets gaan maken, is het veel zuiniger om te 3D-printen. En dan is het ook nog eens sneller, dus we kunnen sneller bouwen en continu verbeteren, en die volgende versie kan veel eerder uitkomen.”
Maar je gebruikte 3D-printen niet alleen voor snelheid, maar ook voor lichtgewicht, om in die ultralichte categorie te blijven.
Matt Chasen: “Dat klopt. We zijn super gefocust op gewicht. Als we te zwaar zijn, zijn we failliet. Het komt dus neer op het benutten van titanium en andere 3D-geprinte metalen. Ik zal Balazs, onze hoofdingenieur, wat meer laten vertellen over wat we hier mogelijk hebben gemaakt. Hij gebruikte benaderingen zoals generatief ontwerp om superlichte structuren te bedenken die gewoon niet mogelijk zijn zonder 3D-printtechnologie.”
Je bent bijzonder trots op het ontwerp van een bepaald onderdeel, de pyloon. Waarom is het onderdeel belangrijk en wat heeft 3DP je ermee laten doen?
Balazs Kerulo: “We hebben een gedistribueerde aandrijflijn. Dat betekent dat we achttien motoren en achttien accu’s hebben. Dat is goed voor de veiligheid, maar het betekent ook dat alles, elk onderdeel dat met de aandrijflijn te maken heeft, met achttien moet worden vermenigvuldigd. Elke gram wordt vermenigvuldigd met achttien. We moeten dus vooral heel efficiënt zijn met het ontwerp van die onderdelen.
De pyloon is waarschijnlijk de belangrijkste van allemaal. Het verbindt de motor met het vliegtuig. Alle krachten gaan er doorheen. Het was een uitdaging om het te ontwerpen om alle krachten, het koppel, de dynamische krachten, enz. te weerstaan. Het was een van de eerste onderdelen waaraan we begonnen te werken en waarvoor we generatief ontwerp gebruikten. We kozen voor titanium en gebruikten vervolgens een materiaal gedefinieerd, generatief ontwerpproces om het te ontwikkelen.
Generatief ontwerp was hier erg handig, omdat we het alleen de beperkingen hoefden te vertellen: de krachten, het koppel en de vermoeidheidskenmerken waar we naar streefden. De computer kwam meteen met een hele goede oplossing die ons beviel en die werkte. En die structuur kon eigenlijk alleen gemaakt worden met 3D-printen.
Omdat de fabricagetechnologie zo nieuw is, gebruiken we zeer hoge veiligheidsfactoren. De veiligheidsfactor die we op dit onderdeel hebben toegepast, ligt rond de tien. Het onderdeel is erg licht en zou nog verder kunnen worden afgeslankt, maar we willen voorlopig bij die hoge veiligheidsfactor blijven. We doen momenteel vermoeidheidstesten met dat onderdeel en als de resultaten goed zijn, kunnen we lager gaan. Maar ja, de onderdelen zijn al zo licht dat we ze misschien moeten laten zoals ze zijn, wetende dat we ze nog verder kunnen verkleinen als we dat ooit zouden willen.”
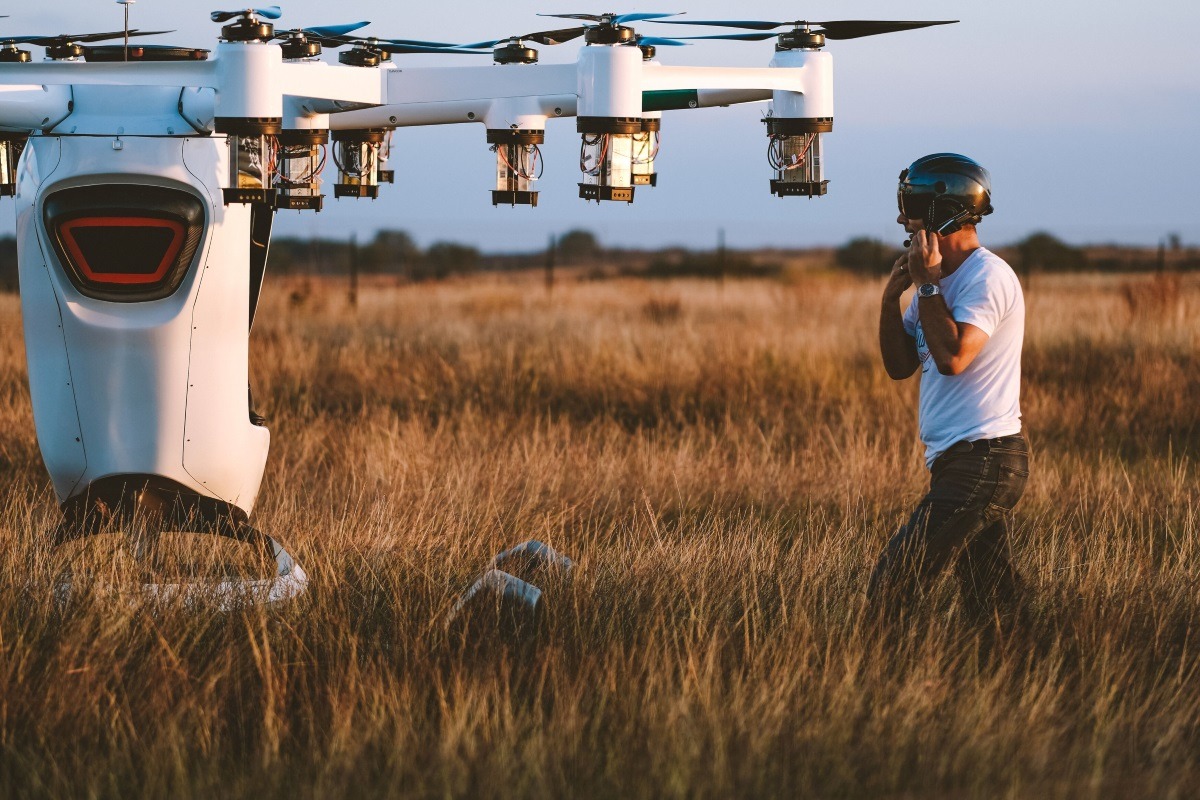
Misschien moeten we op dit punt Charles erbij halen om hem te vragen hoe hij als testpiloot hierover denkt. Laten we beginnen met die veiligheidsfactor tien, die is echt heel hoog voor de luchtvaart.
Charles Justiz: “Tien is behoorlijk hoog. Maar we hebben het nodig omdat we erg licht zijn, dus als we met een lagere veiligheidsfactor wilden gaan, zouden we de structuur op andere plaatsen moeten versterken om trillingen en de gevoeligheid voor lichaamsbuiging te verminderen – en dan plotseling een zwaarder voertuig hebben. We kijken hier naar risico, kosten en gewicht.”
Je hebt dit allemaal bekeken met het oog van een testpiloot. Waar heb je de grootste waarde van 3D-printen in het proces gezien?
Charles Justiz: “Constructiegemak is iets dat mensen altijd noemen als een belangrijk voordeel van 3D-printen, maar het is eigenlijk reconstructiegemak! Als je een prototype van een voertuig hebt en je zegt: ‘Oeps, dat ging niet goed. De belastingsverdeling is niet wat ik had verwacht; de torsie is niet wat ik had verwacht; Ik kreeg turbulentie en het voertuig schudde op deze manier en dat is niet acceptabel, ‘ – je moet het opnieuw doen! Dan kun je zes maanden wachten omdat je een nieuwe mal moet maken om het onderdeel in te gieten of je kunt gaan: ‘Hier is de nieuwe specificatie, CAD/CAM ziet er goed uit, het voldoet aan de behoefte – print die voor mij alsjeblieft.’ In 99,9% van de gevallen krijg je een onderdeel terug dat precies aan je specificaties voldoet. Dat is een enorm voordeel bij snelle prototyping.”
Deze herhaalbare en methodische aanpak lijkt bij jullie alle drie ingebakken te zitten. Het heeft allemaal een snel maar ook heel voorzichtig gevoel. Het is een afgemeten benadering.
Charles Justiz: “We zijn erg snel en erg voorzichtig. Wat erg moeilijk is!”
Matt Chasen: “En dat komt allemaal terug op onze algemene filosofie, die draait om veiligheid. Helemaal in het begin heb ik Balazs uitgedaagd om in de eerste plaats te voldoen aan de ultralichte categorie, maar van daaruit hebben we ons ontwerp volledig geoptimaliseerd voor veiligheid. We hadden bijvoorbeeld geen enkele vereiste om met enige snelheid te vliegen.
We proberen je niet snel een op een bepaalde plaats te krijgen. We optimaliseren voor de ervaring van vliegen in hover en om snel genoeg te gaan om bepaalde dingen te doen. Anderen in de eVTOL-industrie proberen twee dingen goed te doen en dat is heel moeilijk. Om op vleugels te vliegen, maar ook verticaal op te stijgen en te landen. Als je vleugels toevoegt, zijn die vleugels gewoon dood gewicht tijdens het zweven en verminderen ze je veiligheidsfactoren.
Veiligheid loopt door de ontwerpkeuzes, de productietechnologieën en al de andere stappen in het ontwikkelingsproces. Onze missie is vanaf het begin gericht geweest op toegang voor een breed publiek; het is volkomen logisch om eerst voor veiligheid te gaan. Waarom? Omdat elk risico dat je toevoegt, in sync moet zijn met vaardigheden, die vervolgens mensen uitsluiten, en dat is precies wat we proberen te vermijden.” Balazs Kerulo: “We gaan pas iets lanceren als we zeker weten dat we mensen een veilige en boeiende, maar vooral veilige ervaring kunnen bieden. Dat is het punt waarop we de vlucht echt hebben gedemocratiseerd.”